Pressure gauges are essential tools in industries across the world. From manufacturing to healthcare, they play a critical role in measuring the pressure of gases and liquids within systems. Understanding the history, how they work, and how to maintain them ensures that they continue to perform accurately and reliably. Let’s take a deeper dive into these indispensable instruments.
The History of Pressure Gauges
The invention of the pressure gauge dates back to the 17th century. The earliest devices were quite rudimentary, but they were critical in the development of modern science and industry. The first documented pressure measurement tool was the “mercury barometer,” invented by Evangelista Torricelli in 1643. This barometer was used primarily for measuring atmospheric pressure.
In the late 19th century, mechanical pressure gauges evolved, becoming more accurate and widely used. The Bourdon tube, a key innovation, was developed by the French engineer Eugène Bourdon in 1849. His invention revolutionized the industry by allowing for a more precise reading of pressure in various systems.
Over time, pressure gauges have seen significant advancements, from mechanical designs to digital pressure sensors that are now used in many applications. Today, they are found in nearly every industry, from healthcare to aerospace, ensuring systems operate under safe pressure levels.
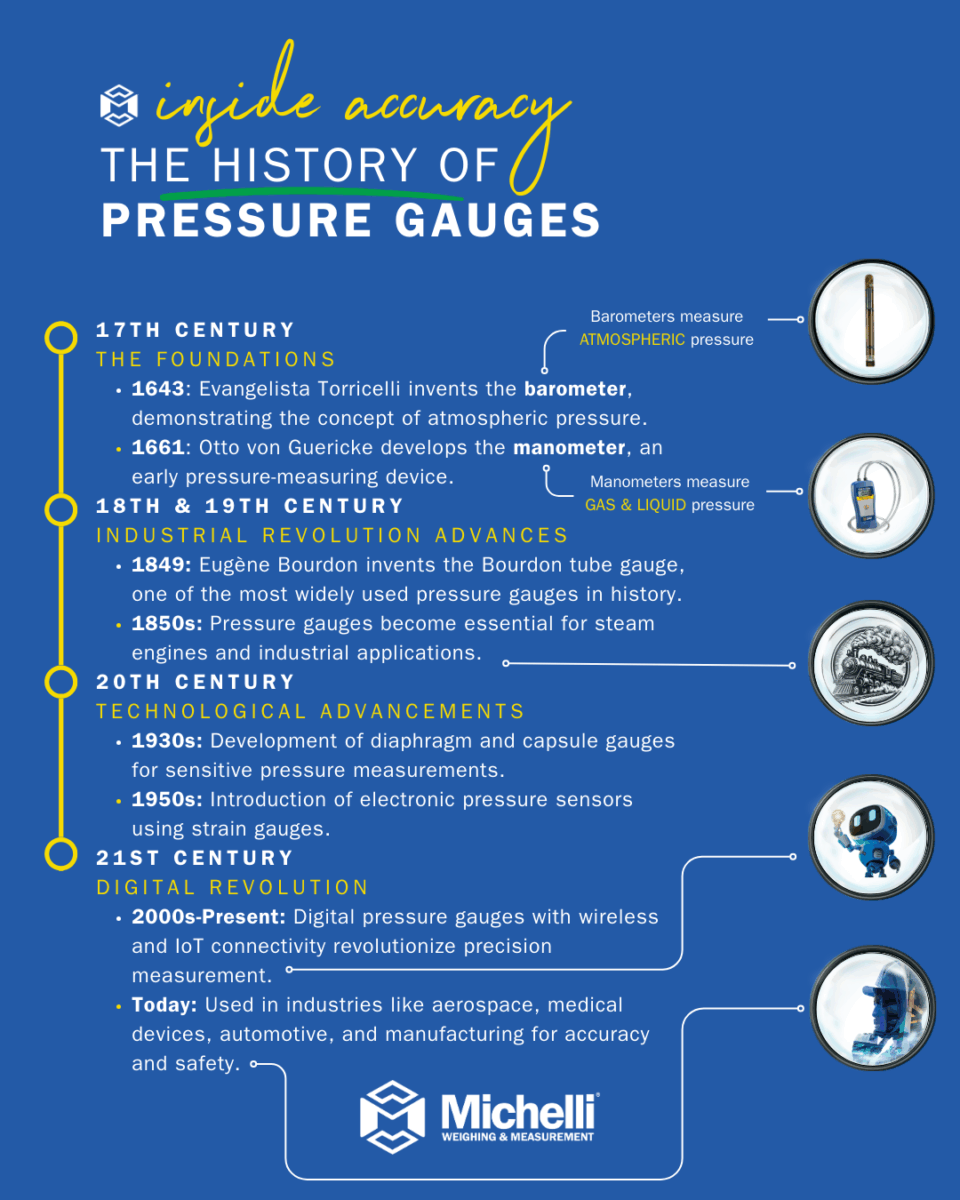
How Pressure Gauges Work
Pressure gauges measure the force exerted by a liquid or gas on the walls of a container, typically a pipe or tank. This force is translated into a readable value on the gauge. Here’s how they typically work:
- Mechanical Gauges (Bourdon Tube): In mechanical pressure gauges, the most common design uses a curved tube known as a Bourdon tube. When pressure is applied, the tube straightens slightly. This movement is transferred to a needle on a dial, giving a pressure reading. These gauges are ideal for applications with medium to high pressures.
- Digital Pressure Gauges: Digital gauges use electronic sensors to measure pressure. These sensors detect the pressure change and convert it into an electrical signal, which is then displayed on a digital screen. These gauges are typically more accurate and easier to read, especially in environments where precise readings are crucial.
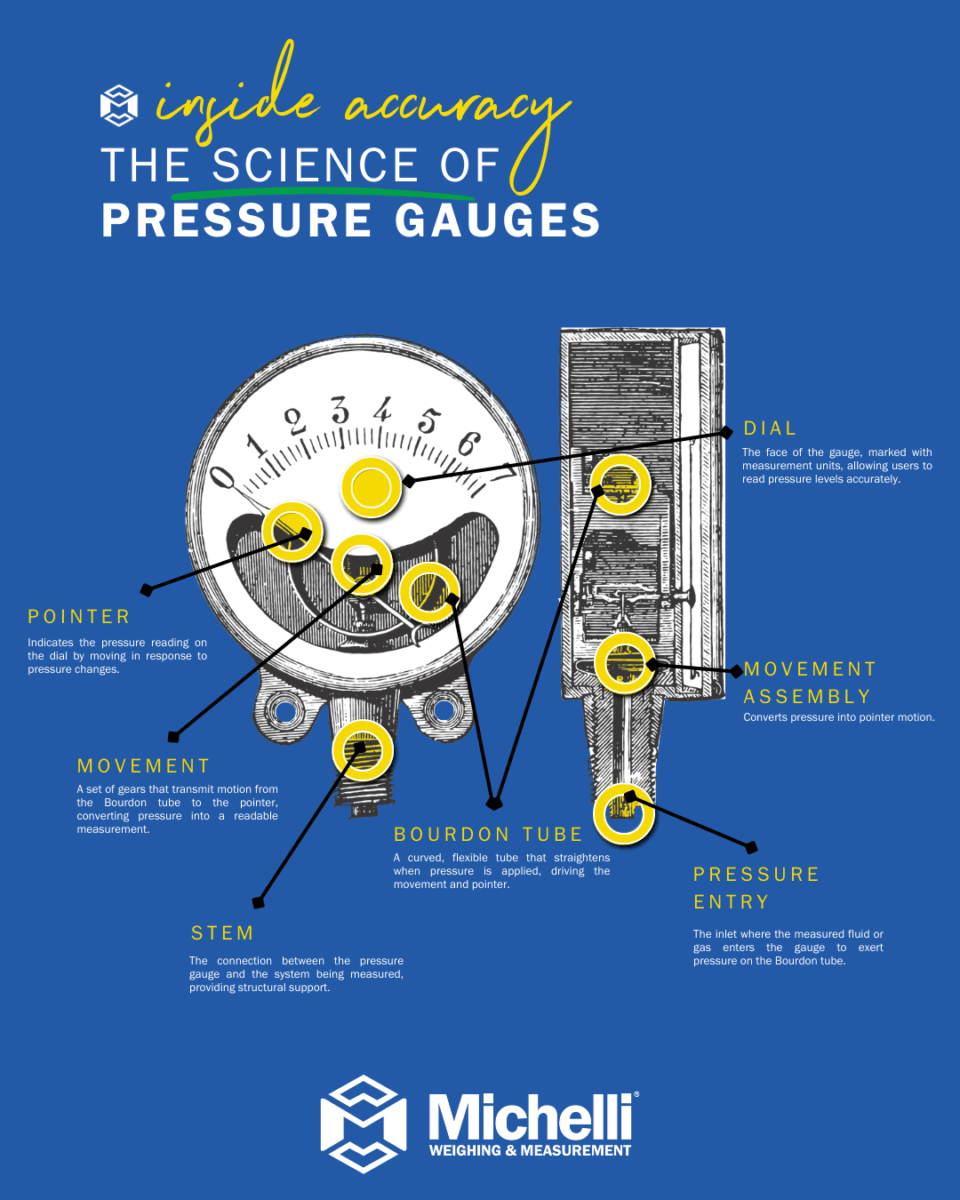
Industries That Use Pressure Gauges
Manufacturing: Pressure gauges are used to monitor systems that deal with hydraulic, pneumatic, or steam systems, ensuring proper operation and safety.
Oil and Gas: In this sector, pressure gauges are vital for monitoring pipeline pressure, drilling equipment, and other machinery to prevent failure and ensure safety.
Automotive: Pressure gauges are used in engine systems to monitor fuel pressure, oil pressure, and other critical aspects of vehicle performance.
Pharmaceuticals & Healthcare: In medical devices like blood pressure monitors, pressure gauges are used to ensure accurate readings for patient diagnostics. Similarly, they are critical in controlling sterilization equipment that requires specific pressure levels.
HVAC: Heating, ventilation, and air conditioning systems use pressure gauges to monitor refrigerant and gas pressures, ensuring that systems run efficiently and safely.
Aerospace & Aviation: In these industries, precise pressure monitoring is required for the safe operation of air and spacecraft, including monitoring cabin pressure and fuel systems.
Calibration of Pressure Gauges
Pressure gauges must be regularly calibrated to maintain their accuracy. Calibration involves comparing the pressure readings of the gauge with a known reference standard. Over time, pressure gauges can drift or lose their accuracy due to factors like wear, age, or damage.
Steps for Calibration:
- Use a Reference Standard: A calibrated master gauge or a deadweight tester is used as a reference to compare the readings of the pressure gauge being tested.
- Adjust the Gauge: If the gauge is not reading accurately, it may need to be adjusted. Some gauges come with adjustment screws for this purpose, but others may require professional calibration.
- Document the Calibration: It’s important to record calibration results for quality assurance purposes, especially in industries with stringent regulations.
Maintaining Pressure Gauges
Proper maintenance ensures that pressure gauges continue to function effectively and provide accurate readings. Here are a few tips for maintaining your pressure gauges:
- Regular Inspections: Visually inspect the gauge for any signs of damage, such as cracks in the face or corrosion. Check for any debris that could obstruct the needle movement.
- Clean the Gauge: Ensure the gauge is free from dirt, oil, or other substances that could affect its accuracy. A clean surface improves the life of the gauge.
- Avoid Overpressure: Never subject a pressure gauge to more pressure than it is rated for. Overpressure can damage the internal components and lead to inaccurate readings or failure.
- Protect from Harsh Environments: If the gauge is used in a corrosive or extreme environment, consider using protective coatings or installing a pressure snubber to reduce vibrations.
- Calibrate Regularly: Regular calibration is essential to maintaining the accuracy of your pressure gauges. How often you calibrate depends on how critical the application is, but it’s typically done annually or semi-annually.
Conclusion
Pressure gauges may seem like simple tools, but they are vital to the safe and efficient operation of many systems. Understanding their history, how they work, and how to maintain them ensures their reliability in industries ranging from manufacturing to healthcare. Regular calibration and careful maintenance are essential for keeping these devices accurate, helping to prevent downtime, improve safety, and extend the life of your equipment. Whether you rely on mechanical or digital gauges, these instruments continue to be a cornerstone of precision measurement in countless applications.
Ready to calibrate your pressure gauges?
Contact Michelli Weighing & Measurement today to ensure your equipment is performing at its best.