Precision is critical in industrial measurement, no matter the industry. Whether you’re weighing raw materials at a sugar mill, tracking inventory in a manufacturing facility, or verifying axle compliance on a truck scale, load cells are the key component making it all possible.
At Michelli Weighing & Measurement, we know how critical it is to choose, install, and maintain the right load cell for your application. Let’s take a closer look at what load cells are, how they work, and why they matter.
What is a Load Cell?
A load cell is a type of transducer—it converts force (typically weight, tension, compression, or pressure) into an electrical signal. This signal can then be read, measured, and interpreted. This is made possible through the use of strain gauges, which are united to the internal structure of the load cell.
When force is applied, the load cell slightly deforms, causing strain gauges to stretch or compress. This mechanical change alters the electrical resistance within the strain gauges, and that change is translated into a proportional voltage signal. That signal is then sent to a device like a scale indicator, Programmable Logic Controller (PLC), or control system for processing.
In industrial environments, precision and reliability are essential—making the choice of the right load cell just as critical.
How they work: Use strain gauges bonded to the body of the cell that deform slightly under load, changing their electrical resistance.
Outlined with a magnifying glass is a picture of a strain gauge—a precision sensor used to measure strain on an object. It’s a critical component in load cells and plays a vital role in accurate weight and force measurement.
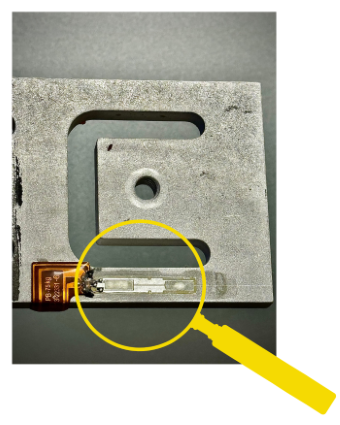
Types of Load Cells
There are many types of load cells, each tailored for specific applications. Here are the most common ones:
Subtypes:
- Single-Point Load Cells
Single point load cells are made to measure weight applied at a single, specific point—making it perfect for platform scales, retail scales, and small hopper weighing. These load cells are ideal for packaging, food processing, and logistics, where precise measurement is essential. - S-Type Load Cells
This load cell gets its name from its design. It’s a versatile load cell that can measure both tension (pulling) and compression (pushing) forces. Inside, strain gauges detect the strain on the “S” beam when a load is applied, converting it into an electrical signal. They’re compact, robust, and suitable for many industrial and laboratory settings. - Bending Beam / Shear Beam Load Cell
Bending and shear beam load cells are compact, precise, and durable solutions for medium-to-heavy weighing tasks—especially where multiple load cells support a structure like a platform or tank. - Double-Ended Shear Beam
Double-ended shear beam load cells are robust, high-capacity sensors ideal for demanding applications like truck and tank scales. Their symmetrical, dual-support design offers superior stability, accuracy, and resistance to harsh loading conditions. - Canister Load Cell
Canister load cells are heavy-duty compression load cells built to handle extreme loads in rugged environments. Their robust design and high capacity make them a standard in vehicle scales, silos, and industrial weigh systems.
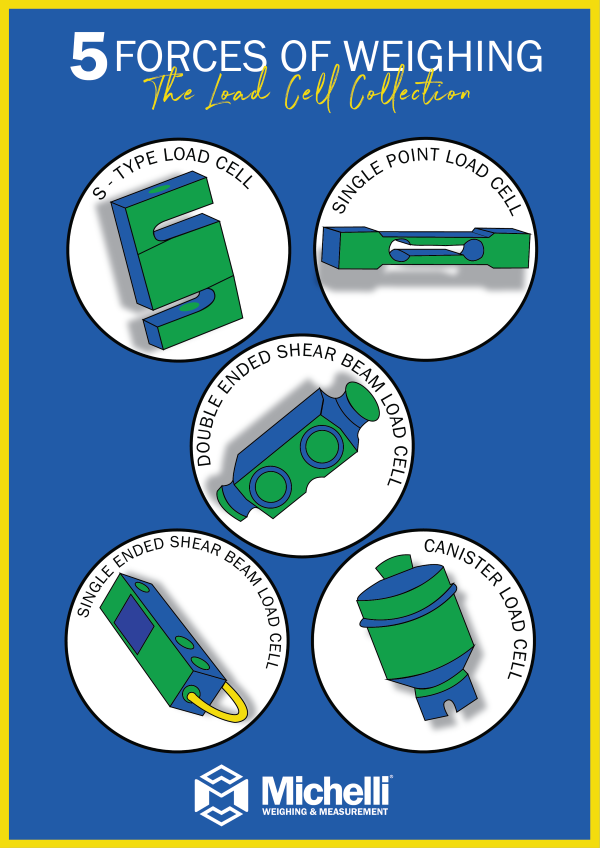
Applications Across Industries
Manufacturing: Batching, blending, process control.
Agriculture: Silo weighing, feed bin monitoring.
Transportation & Logistics: Truck and rail scales, axle load monitoring.
Food & Beverage: Sanitary-scale systems for batching and packaging.
Aerospace & Defense: Component testing, structural load monitoring.
Where precision matters, load cells make it possible!
Choosing the Right Load Cell
When it comes to selecting the right load cell, it takes more than just knowing the weight range. It’s crucial to choose a load cell with a capacity that fits your system’s maximum expected load, including a safety margin. The environment also plays an important role—things like moisture, chemicals, vibration, and temperature extremes affect the choice of materials and seal types.
Accuracy matters as well. For legal-for-trade or mission-critical applications, certified high-accuracy models are essential. Furthermore, keep in mind how the load cell will be mounted and how the force will be applied, since side loads or misalignment can lead to errors. Ultimately, if your application requires certifications like NTEP, OIMOL, or ATEX, be sure to select a load cell that checks these boxes.
Common Challenges—and How to Avoid Them
Load cells are durable, but they can still run into trouble if not properly selected or maintained. Here are a few common issues:
- Signal Drift due to environmental changes.
- Mechanical Misalignment leading to inaccurate readings.
- Overload or Shock Loading, which can permanently damage the sensor.
- Electrical Interference if not properly grounded or shielded.
At Michelli, we routinely help customers troubleshoot these problems—and prevent them with proper setup and training.
Installation & Maintenance Tips
For industries relying on precise weight measurement, maintaining load cell accuracy hinges on a few critical best practices that begin at installation. First, ensure load cells are mounted on clean, level and rigid surfaces, free from vibration or structural deflection, to prevent signal noise and measurement distortion. Proper mounting hardware, such as matched load buttons, clevis assemblies, or self-aligning mounts, should always be used to ensure consistent force transmission and avoid side or moment loading.
Furthermore, calibration and routine maintenance are not just recommended — they are essential for ensuring continued measurement accuracy and process reliability. Over time, even high-quality load cells can experience signal drift due to factors like mechanical fatigue, temperature fluctuations, electrical interference, or minor structural shifts in the mounting system. Without regular calibration, these deviations can accumulate, leading to significant errors in weight readings that may impact product quality, batching accuracy, compliance, or safety. In applications where weighing is tied to inventory control, billing, or automated dosing, even small inaccuracies can translate into substantial operational or financial losses. Scheduled calibrations — ideally traceable to national or international standards — help catch these issues early and validate that your system is still operating within specification. Preventive maintenance routines, including visual inspections, cable integrity checks, and verification of mechanical restraints, can extend the service life of the load cells and minimize unplanned downtime.
Need help installing or servicing a load cell? Our certified technicians across the U.S. can help.
Why Work With Us?
With decades of experience and locations across the country, Michelli Weighing & Measurement offers more than just load cells—we deliver full weighing systems, custom solutions, and on-site support from our corporate headquarters in the greater New Orleans area all the way to your facility, wherever it may be.
Whether you’re upgrading a hopper, solving scale issues, or designing a brand-new process, Michelli brings the expertise you need to achieve unmatched accuracy, maximize efficiency, and stay fully compliant. As your trusted precision partner, we’re committed to empowering your operations—helping you work smarter, faster, and with complete confidence every step of the way.
Got load cell problems?
Contact Michelli Weighing & Measurement today to ensure your load cells are performing at their best.