The Gage Block
Gage blocks are length standards utilized in dimensional measurement. NIST defines the gage block as “a length standard having flat and parallel opposing surfaces”. They are used to produce precise lengths for calibration, or for checking the accuracy of gages, and can be combined by wringing blocks together. Gage blocks provide flat, parallel surfaces with accuracy of few millionths of an inch. They provide lengths in either millimeters (Metric system) or inches (Imperial system). Gage blocks are available in sets to allow users to build any length they would like.
The Gauge Block Handbook by Ted Doiron & John Beers, available on the NIST website, provides the following information regarding atmospheric conditions and the length of gage blocks:
The length of the gauge block is defined at standard reference conditions:
temperature = 20 ºC (68 ºF )
barometric pressure = 101,325 Pa (1 atmosphere)
water vapor pressure = 1,333 Pa (10 mm of mercury)
CO2 content of air = 0.03%.Of these conditions only the temperature has a measurable effect on the physical length of the lock. The other conditions are needed because the primary measurement of gauge block length is a comparison with the wavelength of light. For standard light sources the frequency of the light is constant, but the wavelength is dependent on the temperature, pressure, humidity, and CO2 content of the air.
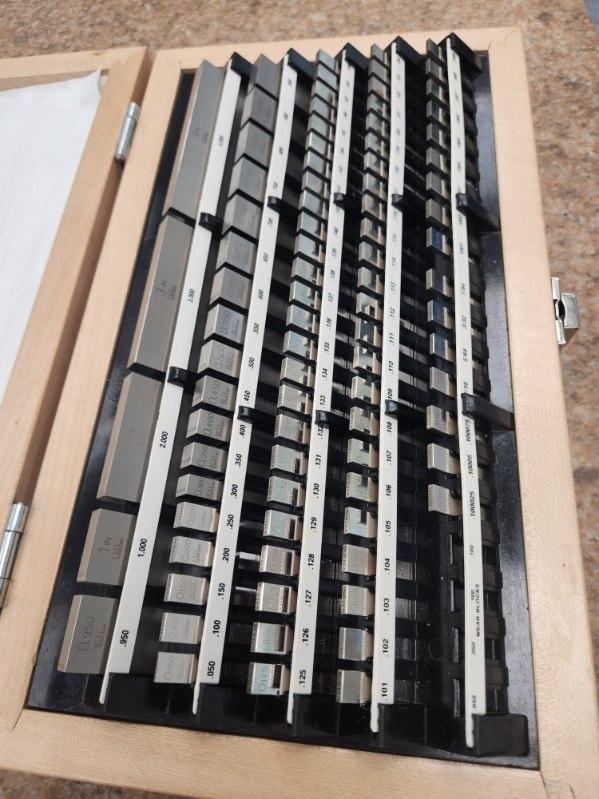
Properties of Gage Blocks
Common Shapes
Gage blocks are available in square or rectangular shapes. The rectangular gage block is the more commonly used Johansson design. Carl Edvard Johansson invented and patented gage block sets in 1896 to be used for length standards in machine shops. These rectangular blocks are also called “Jo-blocks” for that reason.
The square version is known as the Hoke design, and feature a hole in the center. This design was invented by William Hoke in 1917, when he created a cylindrical gage block with a hole in the center.
Wringing
Each gage block is manufactured to a specific thickness, then precision lapped to be both very flat & parallel. Because the block faces are incredibly flat and smooth, they can adhere to one another, or “wring” together without the addition of any type of adhesive. (Although, it is recommended to apply a thin layer of oil when wringing steel blocks together, in order to protect the surfaces.) However, it is important that operators do not leave the blocks wrung together for extended periods of time, as separating could then cause damage to the block faces
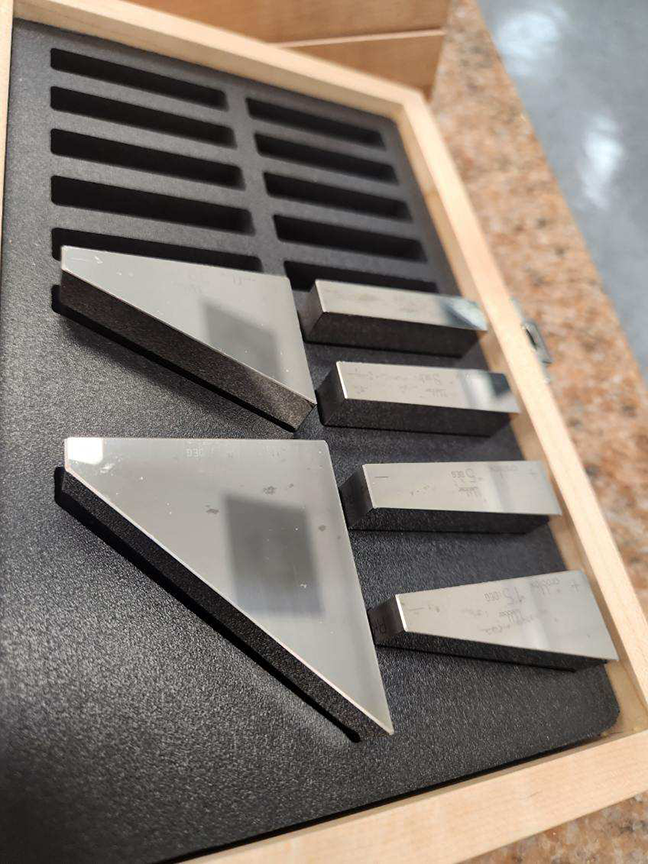
Available Sizes & Measurement Units
Gage blocks are available in millimeters (Metric system) or inches (English system), and are sold in sets to allow users to build desired lengths. These sets should come in a wooden box from the manufacturer, which is also the best place to store them when not in use to prevent damage. Typically, gage block sets include blocks up to 4 inches long. There are also sets available that include blocks measuring up to 20 inches. For sets including blocks with lengths exceeding 20 inches, users will have to place special orders.
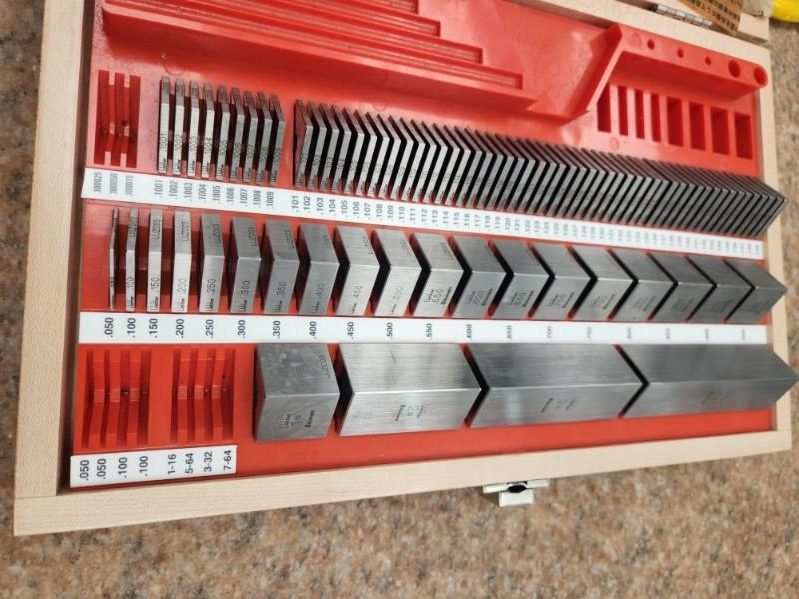
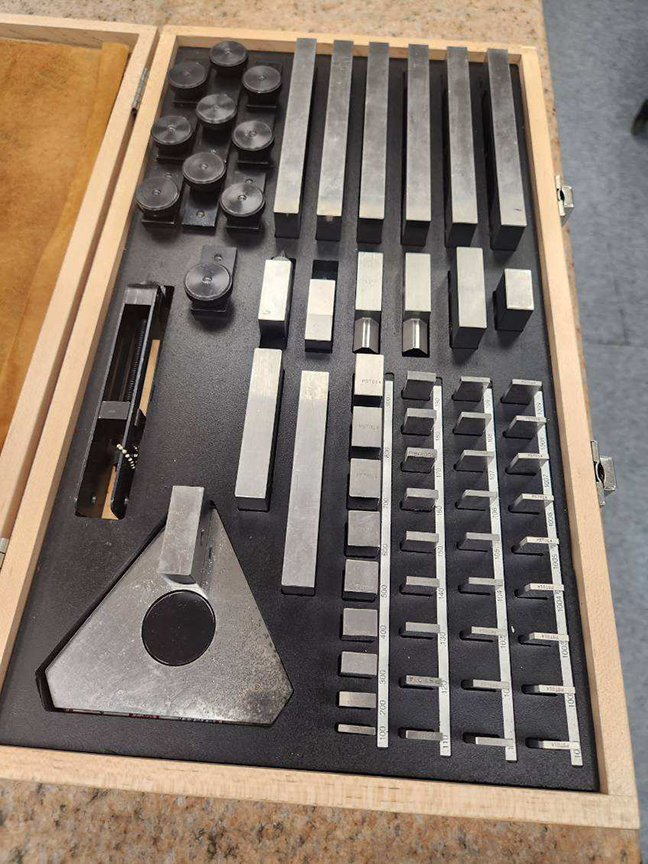
Gage Block Composition
Gage blocks are most commonly made of steel or ceramic. Ceramic blocks do not rust, and do not require the user to wear gloves. Steel gage blocks are the most commonly used. Steel blocks typically cost less than their ceramic counterparts. Many people also prefer steel because the materials with which they are working are also made of steel. So, if a machinist is utilizing a steel gage block to calibrate a caliper that is used to typically used to measure steel bolts, he won’t need to also utilize a thermometer to ensure the measurement accuracy.
However, when using steel gage blocks, operators must wear gloves to avoid transferring oils from their skin onto the block. Also, because steel rusts, it is important to apply a thin coating of oil to the gage block prior to storing it in the case supplied by the manufacturer.
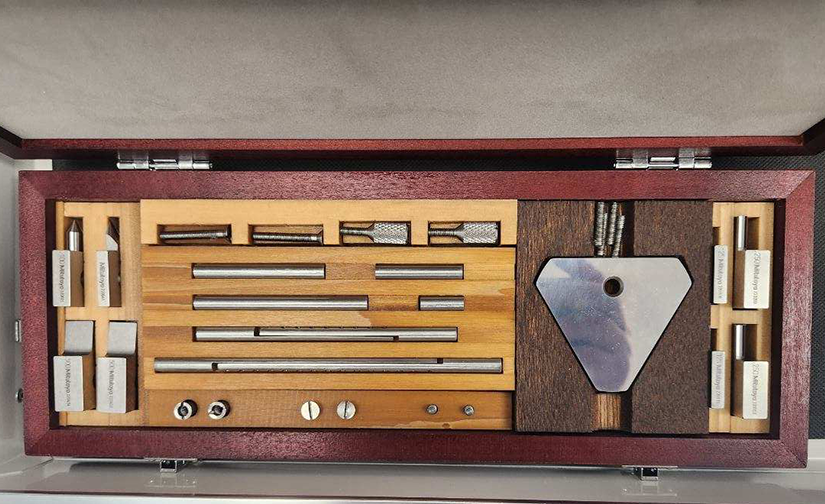
Gage Block Tolerance Grades
Gage blocks are available in 5 tolerance grades: K, 00, 0, AS1 and AS2. Blocks with tolerance grades of 0.5 and 1 have higher accuracies, and are therefore used in calibration lab settings. The grades define tolerances for flatness & parallelism of the block faces, as well as the tolerances for the length of the block itself. Each gage block’s nominal length range fits into a calibration grade (K, 00, 0, AS1 and AS2). Each of those calibration grades has specific limits defined by the ASME as “Limit Deviation of length from Nominal Length” and “Tolerance for Variation in Length” that must be met in order for the gage blocks to be considered within tolerance. Tolerance grades are applicable regardless of the composition or shape of the blocks. To learn more about tolerance grades, please consult the ASME Gage Blocks Standard.
For example, gage blocks of the same length that are all grade zero, have an accuracy of +/- six millionths of an inch. (0.999994 or 1.000006)
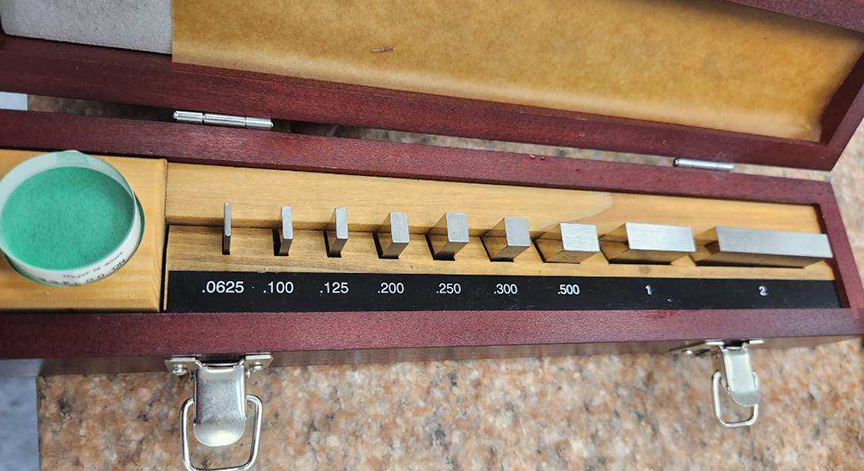
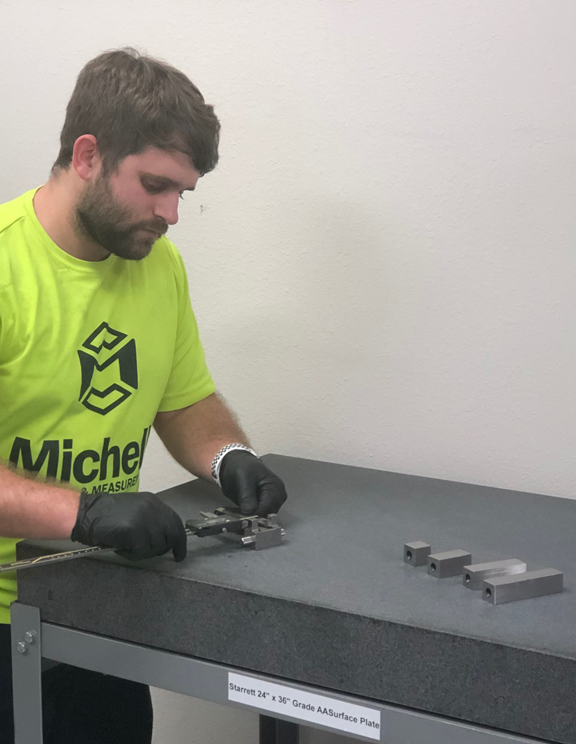
Gage Block Maintenance
It is important to regularly clean gage blocks to remove debris that could scratch or otherwise damage the block faces. It is also imperative to clean the block faces prior to wringing in order to avoid any potential scratches from burs or other debris that may be on the gage block face. Be sure to leave a few hours between the cleaning process and gage block use to ensure their accuracy.
To clean the blocks, NIST recommends immersing them in a bath of an organic solvent such as mineral spirits. The vessel in which you submerge the blocks should have a neoprene bottom to prevent scratches. If necessary, use a soft bristle brush to remove oil. (For Hoke blocks, NIST recommends using a .22 caliber gun cleaning rod to remove oil from the hole.) After cleaning, use a lint free cloth to dry each one. NIST also recommends a second cleaning using ethyl alcohol before wiping with a lint-free cloth again.
When handling gage blocks, take great care to not drop them, which could damage the block face beyond repair. Proper storage is imperative to maintaining the integrity of blocks that are not in use. Gage blocks should be stored in the case provided by the manufacturer, in a temperature-controlled environment. It’s also important to coat steel gage blocks lightly with a rust inhibitor, like machine oil, prior to storing to prevent rust.
For more information on the best way to take care of your precision measurement instruments, visit our blog post Dimensional Tool Care Tips.
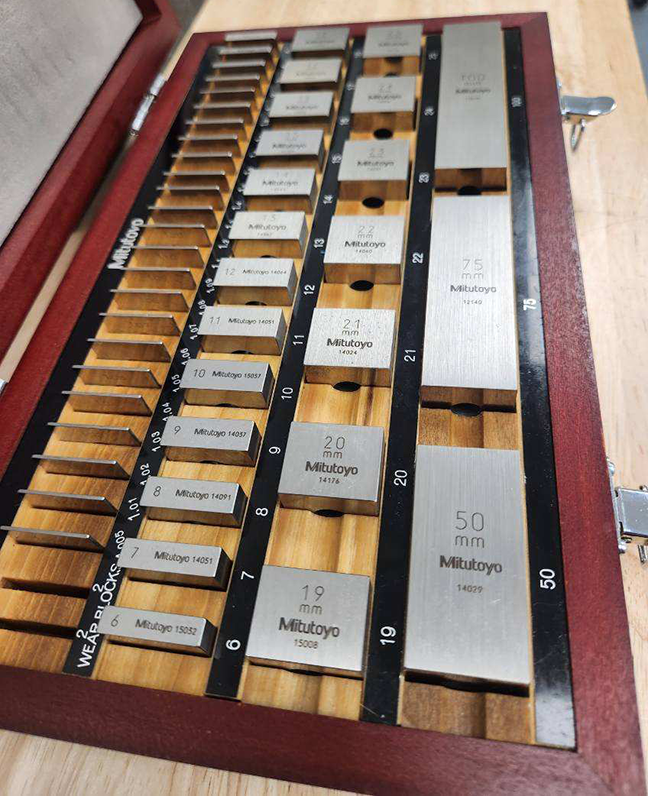
Ready to Purchase a Gage Block Set?
Let the experts at Michelli Weighing & Measurement help you choose the best option for your application. Contact your nearest location today.