If you are doing high pressure, hydraulic calibrations there are a few things that you’ll need to consider which will make your life a little easier and help you produce stable measurements. This application note focuses on considerations for pressure calibrations using a high pressure hydraulic pump to generate the pressure.
Getting Started
To produce stable and high pressure measurements using a hydraulic calibration pump, the gas within the calibration system needs to be removed. Hydraulic test pumps use various types of fluids to generate high pressures. Because gas is much more compressible than liquid, purging most if not all the gas out of the system will allow for maximum pressures to be generated. The following steps describe the procedure to purge the gas from an Additel test pump:
- Ensure the pump, reference standard, and device under test (DUT) are securely connected to the calibration
pump. - Close the vent valve and screw out the main screw press. You
should see a vacuum being pulled on your reference and DUT
(assuming the reference and the DUT are able to be used for
vacuum measurement). - Open the vent valve, wait for the pressure to settle to zero, and
screw in the main screw press. As you do this, you may see
bubbles emerge in the medium reservoir which is a good
indication that gas is being pushed out of the system. - Close the vent valve and repeat steps 2 and 3 one or two more
times. - Close the vent valve and unscrew the main screw press half way
out. Then open the vent valve to zero the measurement. - Now, you are ready to close the vent valve and generate pressure.
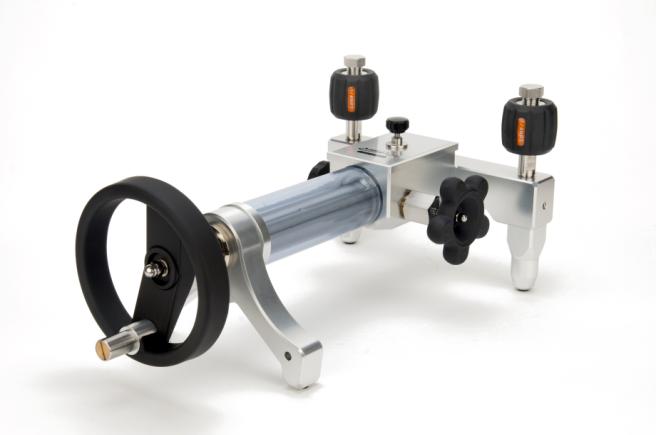
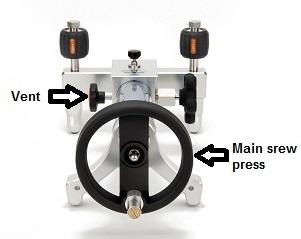
Stable Measurements
As pressures are generated to the desired test point it is common to initially observe a fairly rapid decrease in pressure. Initially, you may conclude that this is a pressure leak but what you are likely observing is called the adiabatic effect. This effect is defined as a gain or loss of heat within a system and its environment. When a gas is compressed under adiabatic conditions, its pressure increases and its temperature rises without the gain or loss of any heat. This happens when the screw press of a pump compresses the fluid volume, thus resulting in an increase in pressure but also an increase in the temperature. As the increase in pressure stops the temperature generated from the screw press dissipates. If the volume is held constant and the temperature decreases so also will the pressure decrease. So this initial degrease of pressure is in fact a result of the temperature settling from the adiabatic heating effect generated from the screw press of the pump.
Other sources of instability that also impact the pressure measurement are instabilities in room temperature and changes in volume. Because temperature is a factor of pressure as the entire pressure system changes temperature due to the room temperature changing the true pressure value will also change. The same can also be said of the pressure volume. With an increase or decrease of pressure volume the true pressure value will see a correlated change. Volume changes with pressure systems are usually not very noticeable except at high pressures. At high pressures, the materials where the pressurized volume is contained will slightly expand causing the volume to expand and the pressure will decrease. This is particularly evident when using flexible hoses at high pressures.
Conclusion
So we can’t change the laws of physics—so what can be done? As pressures are generated, time must be given to allow for the adiabatic effects to settle. In other words, you need to let the measurement stabilize for a few minutes. As you allow this stabilization period to happen, you’ll find the measurement stability of the pump to be very reliable for your calibration applications. Room temperature will also have an impact on the measurement and it is best if calibrations are performed in a controlled, stable environment. Lastly, careful consideration of hoses, manifolds, and tubing will help produce stable results at high pressures. Using metal tubing as opposed to flexible hoses will yield higher stability as metal is less likely to allow for the volume to expand when under high pressure.
We hope you found this application note to be helpful. Specifically, it can be helpful with any of Additel’s hydraulic pumps to help you achieve the best measurement results possible. For more information please contact us (PH: 1-714-998-6899, E: [email protected]) or visit us on the web at www.additel.com
Additel Corporation is a premier, worldwide provider of process calibration equipment. We are dedicated to designing, manufacturing, and delivering the highest quality handheld test tools and portable calibrators for process and calibration industries. For many years, Additel has successfully developed automated pressure calibrators, digital pressure test gauges, digital pressure calibrators, pressure test and calibration pumps, and multifunction process calibrators. In recent years, we have expanded the calibration equipment we have for sale with temperature calibration tools that help make metrology simpler.
The above post was written by Jon Sanders, with Additel Corporation.
Need Hydraulic Pressure Calibration Equipment?
Contact your local Michelli Weighing & Measurement team of experts today. We can help you find the Additel hydraulic pressure calibration equipment you need.