Incorporating weighing & measurement equipment into existing processes can help increase efficiency
The addition of scales, in-motion checkweighers, weighing systems & other measurement equipment to existing machinery allows users to combine weighing with existing operations. This combination increases efficiency by reducing the amount of time & effort required to complete a task. Incorporating weighing & measurement equipment can also enhance quality control operations & make data collection a breeze.
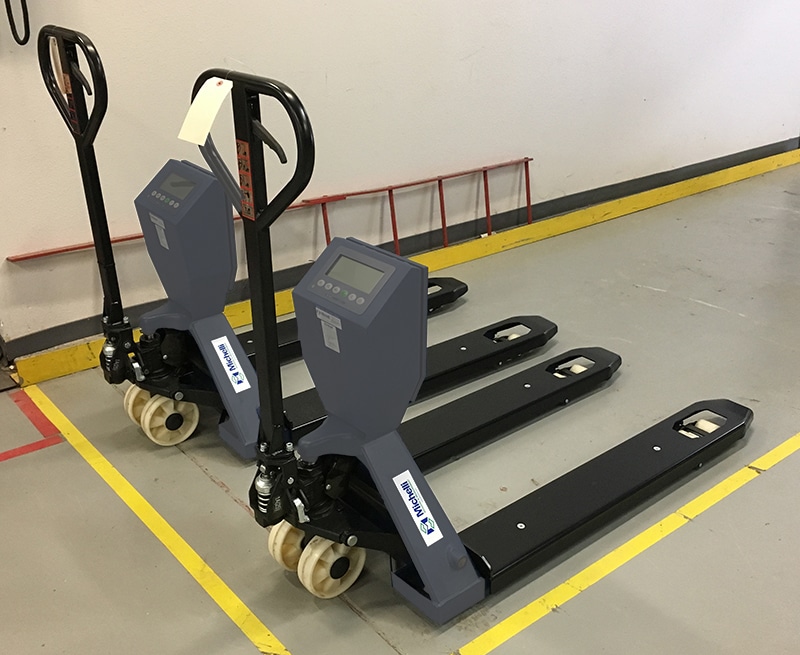
Using Pallet Jack Scales & Forklift Sales (Lift Truck Scales) to Maximize Efficiency
For example, a traditional lift truck or pallet jack is used to move heavy items from one place to another. In order to weigh the package, a staff member must use a forklift or pallet jack to move it over to the scale. Then, the package needs to be placed onto the scale to collect weight, before returning it to the pallet jack, or picking it up with the forklift to transport it again.
If the same employee uses a pallet jack scale or forklift scale to move the package, he/she can collect weight data during transport. By adding a lift truck scale to your existing forklift, or utilizing a pallet jack scale, you can move and weigh the product at the same time, cutting time & effort in half, therefore increasing efficiency.
Increase Efficiency with In-Motion Checkweighers
While weighing & measurement equipment can help companies save time, it can also enable semi-automated processes to reduce production bottlenecks. Incorporating weighing & measurement equipment is a great way for organizations to streamline quality control operations.
For instance, in-motion checkweighers give users the power to greatly increase efficiency. By automating the quality control process, production requires less time & human interaction. Consider packaged meat moving down a conveyor. Without incorporating a scale into the operation, quality control employees would need to remove the meat from the conveyor, weigh it to make sure it is within the target weight range, then return the meat to the conveyor to proceed to the next phase of processing.
By incorporating an in-motion checkweigher and setting a target weight range, the packaged meat could flow down the conveyor & automatically undergo a quality assurance check. The check would determine whether or not each package was within the target weight range. If not, the in-motion checkweigher would reject the product. So any package that was above or below the target weight range could be removed from the line without interruption to the operation, and with minimal interaction from the staff.
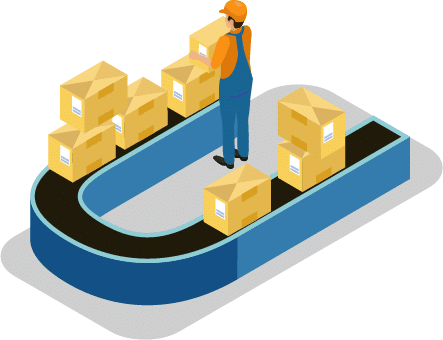
Conveyor Scales for Quality Control & Efficiency
Conveyor scales are another “add-on” that can increase efficiency & help ensure quality. With the help of a conveyor scale, organizations can calculate the total amount of material produced in an hour, a shift, or a day to help measure & record productivity, yield & other metrics. Conveyor scales can also be integrated with label printing operations.
Imagine a conveyor scale used in an aggregate plant that produces crushed stone. The conveyor scale could measure the amount of stone produced during each shift, and during each day. The management team could then base production forecasts on the average amount of crushed stone produced during 1 buying cycle. That information might be used to give completion dates to prospective buyers, or to help managers discover the time of day when something went wrong, such as a machine failure.
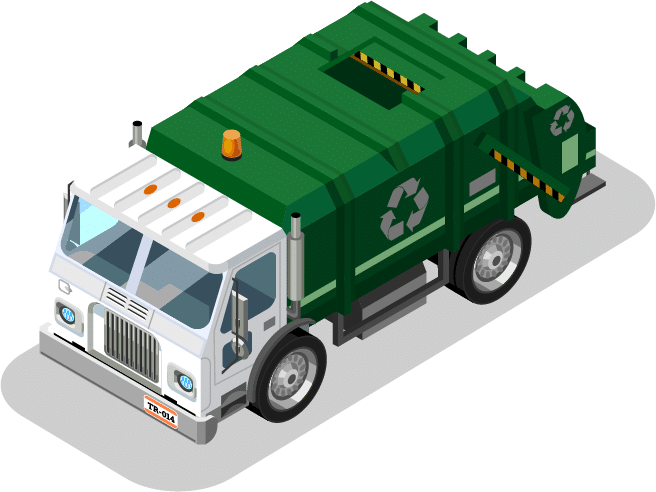
On-Board Weighing Equipment Enables Weight Monitoring During Loading
On-board weighing is a huge advancement for the measurement industry. With on-board weighing, organizations can install scales on dump trucks, transport trucks and more. These scales enable drivers to monitor weight as their trucks are loaded, instead of leaving the loading dock to find a truck scale, then potentially needing to return to the loading dock because they are under weight or over weight. This is especially useful in the food/beverage industry, waste/recycling industry, and the chemical/petrochemical industry.
Let’s look at how on-board weighing helps increase efficiency in the waste/recycling industry. Customers are often charged by the weight of waste material in their dumpsters. On-board weighing helps waste & recycling companies track each dumpster’s weight throughout the day. As each receptacle is emptied, the weight of the material inside can be recorded. The total weight collected can then be verified at the end of the shift, and customers can be billed accordingly.
Please note: Most on-board weighing systems are non-certified, and therefore not legal-for-trade. So while the on-board weighing systems are a fantastic tool to use to increase efficiency during regular operations, they will not replace a certified, legal-for-trade truck scale.
Incorporating Data Collection to Maximize Efficiency
Some weighing & measurement equipment is programmable & makes data collection possible. In those situations, the addition of weighing & measurement equipment to existing processes can not only increase efficiency, but can also enable recording features to monitor production. Measurement gear can be used to gather data & update records, without an operator ever lifting a finger.
For example, a data collection weighing system coupled with a truck scale might enable operators to pull information on each and every truck that ran across the scale within a day, or even an hour, effortlessly. These systems can be customized to require driver names, take pictures of license plates, and even store company information for customers who may pay their weigh-in bill monthly. These types of systems allow scale operators to monitor truck scale use while cutting out manual record keeping, so they can focus on more important tasks.
Some conveyor scales & in-motion checkweighers can be programmed to record data as well. This function allows management teams to monitor yield, waste, and productivity. The custom program could be set up to record the information in a password-protected spreadsheet, that is made accessible to multiple users.
There are many ways to incorporate weighing & measurement equipment into existing processes to maximize efficiency. The possibilities are limitless. Speak with a Michelli Weighing & Measurement expert today to discuss ways you could use equipment to work smarter, not harder.
Ready to maximize efficiency in your organization?
Contact your local Michelli Weighing & Measurement location to speak with an account manager. We will get a better understanding of your operation, then work with you to discover ways you could incorporate weighing & measurement equipment to make your work day easier, safer & more productive.